The projects and the results in recent five year
1.鐵水溶碳模式
廢鋼應用在轉爐煉鋼製程是必然的趨勢,而碳溶解至鋼液的速率對製程時間影響很大,因此吾人以數值模型探討碳溶解速率。研究中發現在高雷諾數(Re)下,在碳粒後方會有迴流區,造成在流場分離點位置,溶出速率最低,在前停滯流點最高,後停滯流點次之;在低雷諾數下,碳粒後方沒有迴流區,因此碳粒溶出速率在前停滯流點最高,往後停滯流點位置逐漸減少。顆粒表面的質量溶解速率分佈,明顯受到回流區大小、流場流速和擴散速率的影響。利用准穩態(qusi-steady state)溶碳過程的假設,模擬不同狀態下的碳粒溶解速率,將數值模擬獲得之Sherwood數與主導流場之Reynolds和Schmidt數,利用曲線擬合建構一簡化溶碳關係式。吾人也建立一個動態縮減模型,比較兩者溶解時間之差異,可作為減化方程式修正之參考。此外,從動態縮減的模擬結果也發現,在溶解過程碳粒會改變其形狀,之後維持其相似性(self similarity)變小。
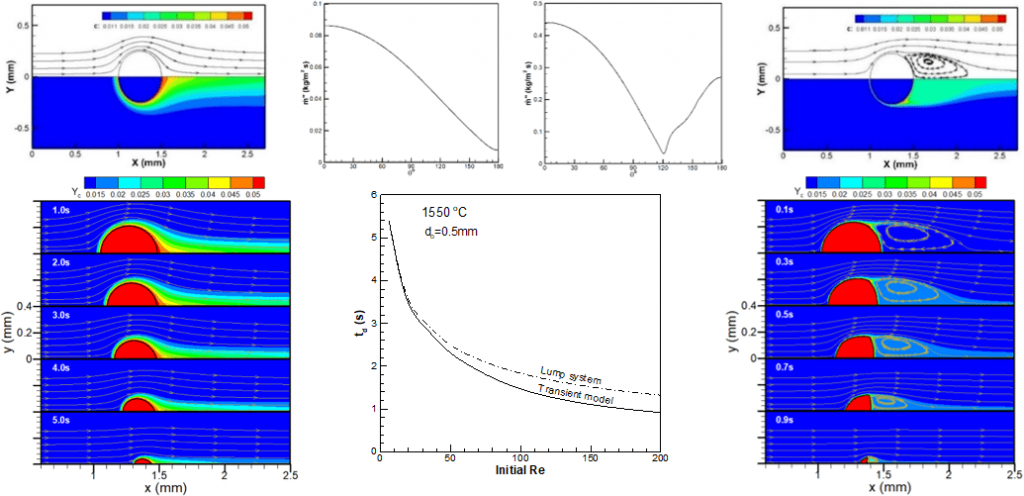
2.廢輪胎導入廢鋼製程之模式建立與模擬
A transient 3-D numerical model has been successfully built to investigate the turbulent tire burning process in a furnace. The turbulence k-ε model and the combustion finite-rate/eddy-dissipation model are used to simulate the tire burning in hot furnace. The batch of tyre pieces is tossed in the furnace by using the discrete phase model (DPM) with spherical shape. The results show that the pyrolysis rate of a tyre piece will quickly reach a certain rate and maintain constant in a hot furnace of high temperatures. The pyrolysis time and the combustion efficiency increase with a larger size of tire. In addition, the pyrolysis time increases with a heavier tire batch as well, but the combustion efficiency decreases. More top-injection oxygen consumed by liquid iron causes less oxygen in the furnace, and consequently results in less combustion heat release and longer pyrolysis time of tyre pieces. Furthermore, the influences of the distribution of tyre pieces and different turbulence models were also investigated in this study.
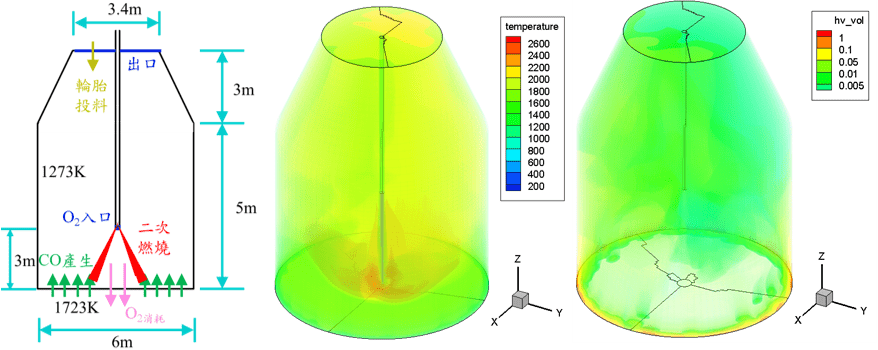
3.突擴流道內火焰行為分析
Flame behaviors in a mesoscale one-stepped sudden-expansion channel are numerically investigated by a two-dimensional model without symmetry assumption at centerline. The channel expansion ratio is equal to 2. The isothermal wall boundary condition (300K) is set to eliminate the wall-flame thermal interaction. It is found four flame behaviors: the steady mushroom-shaped flame, the steady tulip-shaped flame, the periodically oscillating flame and the randomly oscillating flame. The steady tulip-shaped flame can be stabilized due to the wall quenching effect of the sudden-expansion step. The periodically oscillating flame occurs is due to the second Landau-Darrieus instability. In addition, the existence of the complex oscillating flame is attributed to the interaction of Landau-Darrieus flame instability and the hydrodynamic instability of the sudden-expansion channel itself.

4.膨脹防火塗料模型
In this study, a new model for intumescent coatings is developed including the radiation transfer equation. So, one of the important features of this model is to give the insight of the radiative heat transfer in the intumescent coating during expansion. In addition, the model equations are derived into a new coordinate system by introducing the expansion effect into the corresponding parameters. Consequently, the numerical results can be carried out by using a fixed grid system. The numerical results show that the radiative heat transfer near the exposed coating surface cannot be well simulated by the model of thermal radiation conductivity, which is widely used in the previous studies. So, it is suggested that the radiative heat transfer in the expanded char region should be formulated by a more considerate model. The established model was also used to investigate the effect of different heat source combination on the intumescent coating performance.
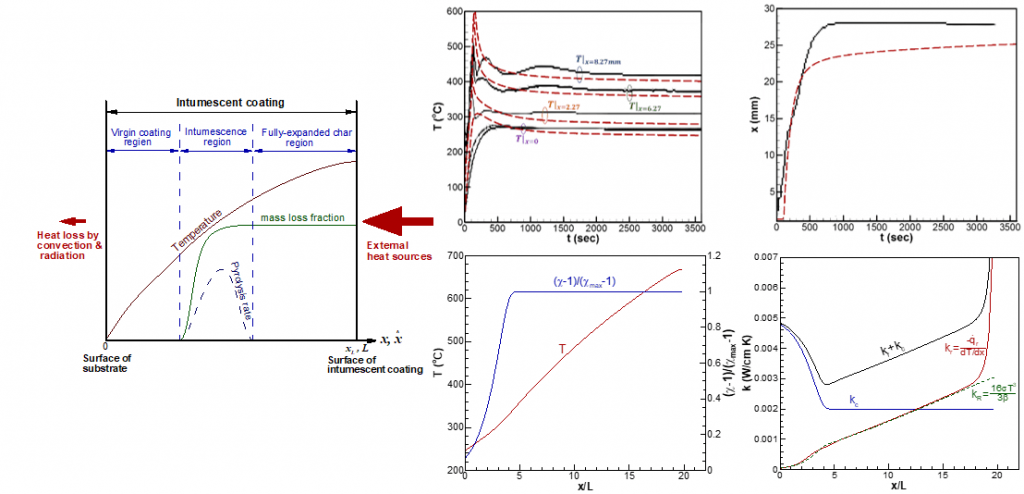
5.太陽能板製程模擬
本案利用熱流分析模型,對銅銦鎵硒(Copper Indium Gallium Selenium ,簡稱CIGS)薄膜太陽能板,在硒化鍍膜製程中的流場變化、溫度分佈以及硒化氣體擴散進行模擬,協助廠商對製程腔體內部熱流場的了解,並分析太陽能板表面鍍膜反應不均的原因。同時,也探討加入強制對流(風扇)對提升鍍膜品質的可行性,並提供其他提升腔內均溫性的方法,且利用模擬加以分析其結果。透過數值模擬分析提升廠商對製程技術的了解,並協助未來製程空腔的設計,可有效降低研發成本提升產品良率。
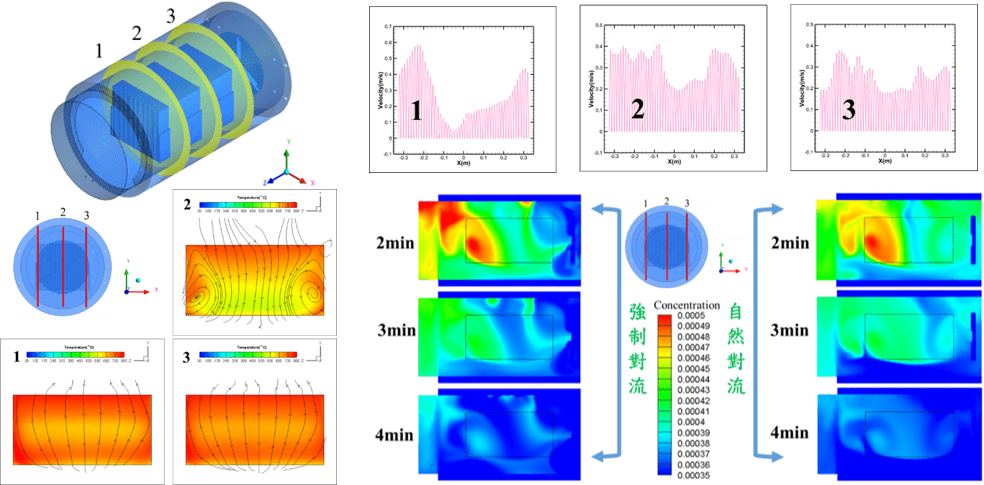
6.轉爐頂吹分析與頂底同吹模型建立
頂底同吹是轉爐全廢鋼製程中不可或缺之技術,本研究成功建立頂吹氧槍模型,並用以分析不同氧槍設計及操作下,對鋼液攪拌動量、爐內爐壁噴濺量、損失量、黏槍量等之影響,提供頂吹氧槍枝設計及操作參考。研究亦成功建立頂底同吹之轉爐模型,模型中考慮底吹氣體(甲烷、氧氣)及碳粒在鋼液中的化學反應與溶解現象,並且模擬底吹可燃氣體在爐內的二次燃燒反應,完整模擬轉爐頂底同吹之熱流場,因此模擬結果可協助了解轉爐工作時之內部熱流場,對製程的分析及操作非常有幫助。
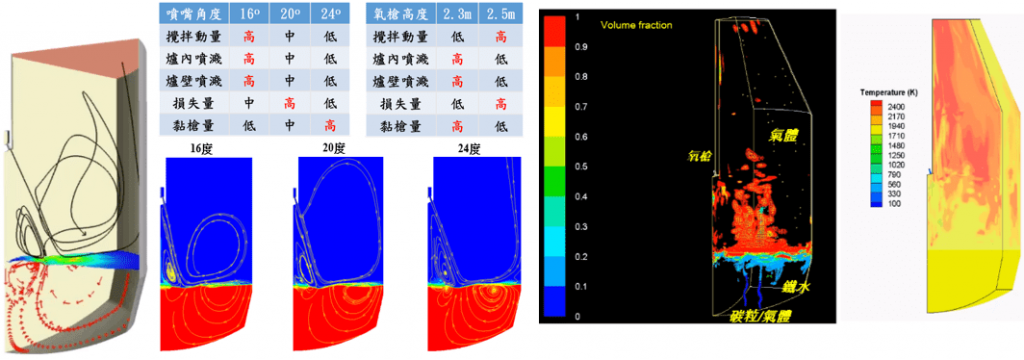
7.水模底吹侵蝕分析
研究以二相流VOF模型模擬中鋼水模底吹侵蝕實驗,測試不同流量下,底吹管附近壁面受到水滴回擊的破壞程度。模擬結果與實驗數據比較發現,在破壞範圍及程度上,二者具有良好的一致性。低流量時,侵蝕破壞範圍隨底吹流量而增加;然而,當流量大至某一流量時,破壞範圍會變小。模擬結果進一步顯示,當流速增加至破壞範圍縮小,其在中間位置之破壞仍隨著流速增加而增加。本研究所建立之模型獲得水模實驗驗證,可進一步模擬轉爐煉鋼之底吹條件,模擬分析底吹流量對爐壁破壞的影響,提供現場操作參考,增加轉爐爐壁使用壽命。
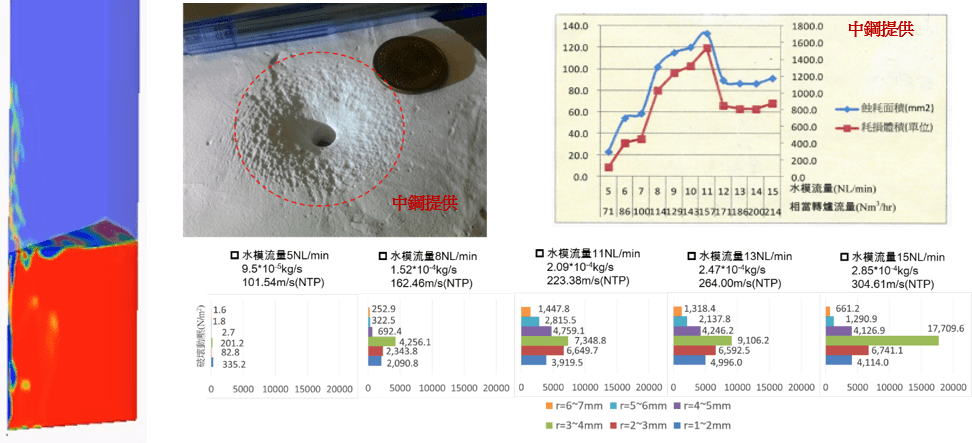